This abap programming report in sap provides a list of all components in a bill of material (BOM). The BOM lists in an indented format to illustrate the hierarchical relationship among the assemblies and components. You can use this report to provide a quick display of the structure at any point to analyze a parent/child relationship and the potential impact of changes.
No prerequisites are required to run this report. The system provides several application codes (for example, transaction OS30) which are already configured to select and filter among any alternative BOMs for 1 the material. It is possible to add to these codes, or to modify the settings, but it is generally not necessary.
You can choose selection criteria based on the functional purpose (for example, inventory management), costing, production, etc. For example, if you choose to use Engineering Change Management (ECM) and a specific Engineering Change Number (ECN) is involved, the display may optionally be restricted to a given ECN.
From the display, you can view additional information about the item on the BOM, including any scrap factors, co-product indicator, offset lead-time, component discontinuation data, and ECNs.
In addition, you can branch from the first screen of the report and apply additional filters such as the item category, item status, and material provision indicators, as well as scrap calculations. You can choose menu options to branch to the material master of the component, as well as to the display of a where-used list for the component.
From the indented listing, you may print the results or view a graphical display of the BOM by choosing Goto → Graphics.Additionally, a given component may be selected and the following functions invoked:
1. Display of the general data view of BOM component, including scrap factors, co-product indicator, offset lead-time, component discontinuation and ECN (Goto → Item data). From this point it is possible to branch throughout the BOM display.
2. Display of the material master for the component (Environment → Detail)
3. Callup of a where-used list for the component (Environment → Where-used list)
4. Display of the selection criteria used to perform the display (Extras → Selection criteria)
To access the first screen for this report, choose Logistics → Production → Master data → Bills of material → Reporting → BOM explosion → Multi-level BOM.
1. Enter a material (for example, P-100) in Material.
2. Enter a plant (for example, 3000) in Plant.
3. Enter BEST in BOM application.
BEST is the German abbreviation for inventory management.
4. If required, enter a past or future effective date. TheValid from field will default to the current date. Leave the other fields blank unless a specific ECN number or revision level is required.
5. If Required quantity is left blank, it defaults to 1.
6. Choose Execute.

A Level number for the component within the BOM (numbering and indentation illustrate the parent/child relationship)
B Component number and description.
C Number of subassembly components needed to produce the desired components
D Item category (for example, L = stock item, D = document)
7. To find out where a given component might be used, position the cursor on the desired line and choose Environment → Where-used list.
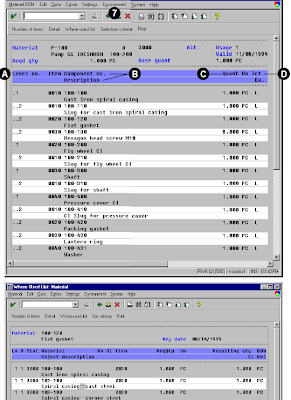
2. Choose Execute.
This filter allows you to change the display of the previous example.
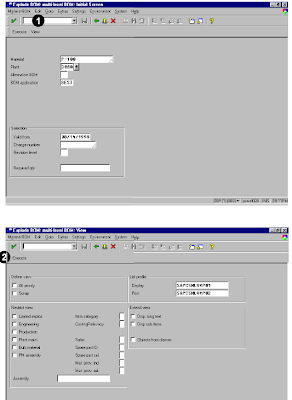