SAP programming report for back order processing is related to the Missing Parts Info System,this report displays all requirements for a given material and allows you to change prior commitment quantities.A planner would use this report to quickly assess demands and reallocate materials among manufacturing orders based on changing priorities and inventory availability.
The data displayed in backorder processing is based on commitments which are generally done automatically during order creation or release. Additional demand information will be reflected based on SD order allocations and the last MRP/MPS run. Consequently, backorder processing needs to consider this to ensure visibility of all potential demands. Backorder processing relies on the availability checking rules maintained in configuration and referenced on the MRP and sales view of the material master.
You can run backorder processing from the Missing Parts Info System, or call it up directly from the menu.
You can change the commitment quantity from the first screen within backorder processing. The menu options let you:
- Branch to the stock overview
- Display the individual demand element from MRP
- Peg to upper-level demand
- Drill down to dependent requirements
From the first screen, you can change the commitment quantity for a given demand either by choosing Change confirmation, or by choosing Edit → Change confirmation.
Other actions which may be taken from the menus or icons are as follows:
1. Save all changed commitment quantities (reallocations) (Backorder processing →Save).
2 Display Scope of Check to verify sources of demand and supply being considered in the check (Goto → Display scope of check; icon also available).
3. Filter the demands to show only SD requirements, reservations for production orders, or both (Settings menu).
4. Switch to columns reflecting receipts, demands, etc. by period (Settings →Period totals; icon also available).
5. Branch to the Stock Overview screen for the material (Settings → Stock overview).
6. Display the individual demand element (MRP element) (Environment → Disp MRP element).
7. Display pegging to upper-level demand or lower-level dependent requirements (Environment → Pegging or Order report; icons available).
To access the first screen for this report, choose Logistics → Production → Production control → Control → Backorder processing → Material
1. Enter 100-100 in Material.
2. Enter 3000 in Plant.
3. Enter PP in Checking rule.Checking rule PP is typically used for manufacturing orders.
4. Choose Enter.

A Demand by date and source
B Committed quantity
C Cumulative ATP quantity
5. Choose Period totals to reformat the screen.
The screen is reformatted to bucket demand and supply by time periods.Time buckets may be changed using the icons provided on the toolbar.
D The Scope of check may be displayed using the icon.

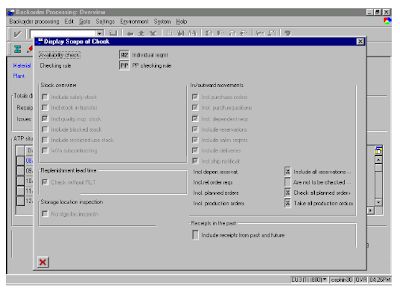
abap programming report on missing information
No comments :
Post a Comment